Alăturați-vă echipajului RAN Sailing ~ pentru streamuri live, conținut exclusiv și multe altele https://www.patreon.com/ransailing Viața din culise a fost grea în ultima vreme, dar pe ecran am primit primele scânduri pe carenă și Johan face un test pentru a vedea ce tip de îmbinare a eșarfei va fi cel mai bun. Suntem o familie suedeză care a navigat prin lume din 2016 în timp ce împărtășim aventurile aici pe YouTube. În timp ce încă navigăm, obiectivul nostru principal acum este construirea RAN III, o barcă cu pânze de 50 de picioare pe care o construim de la zero. Postăm un episod nou în fiecare vineri, așa că asigurați-vă că vă abonați și apăsați clopoțelul pentru a fi primul care află când există un nou episod! CONECTAȚI-VĂ CU NOI – Site: http://ransailing.se – Instagram: http://www.instagram.com/ransailing – Facebook: http://www.facebook.com/ransailing PRODUSE ȘI CAMERA: https:// www.amazon.com/shop/ransailing Am adunat unele dintre produsele pe care le folosim în viața noastră de croazieră și realizarea de videoclipuri în magazinul nostru Amazon. Dacă cumpărați oricare dintre articolele din magazinul nostru, primim un mic „ka-ching” în pisicuța noastră de croazieră (fără costuri suplimentare pentru dvs.). Mulțumesc mult și mulțumesc programului Amazon Influencer. Credite muzicale: http://www.epidemicsound.com Love, Malin, Johan & Vera
source
Prima dintre cele 150 de scânduri de bandă | Barcă cu pânze DIY 50 ft – Ep. 344 RAN Sailing
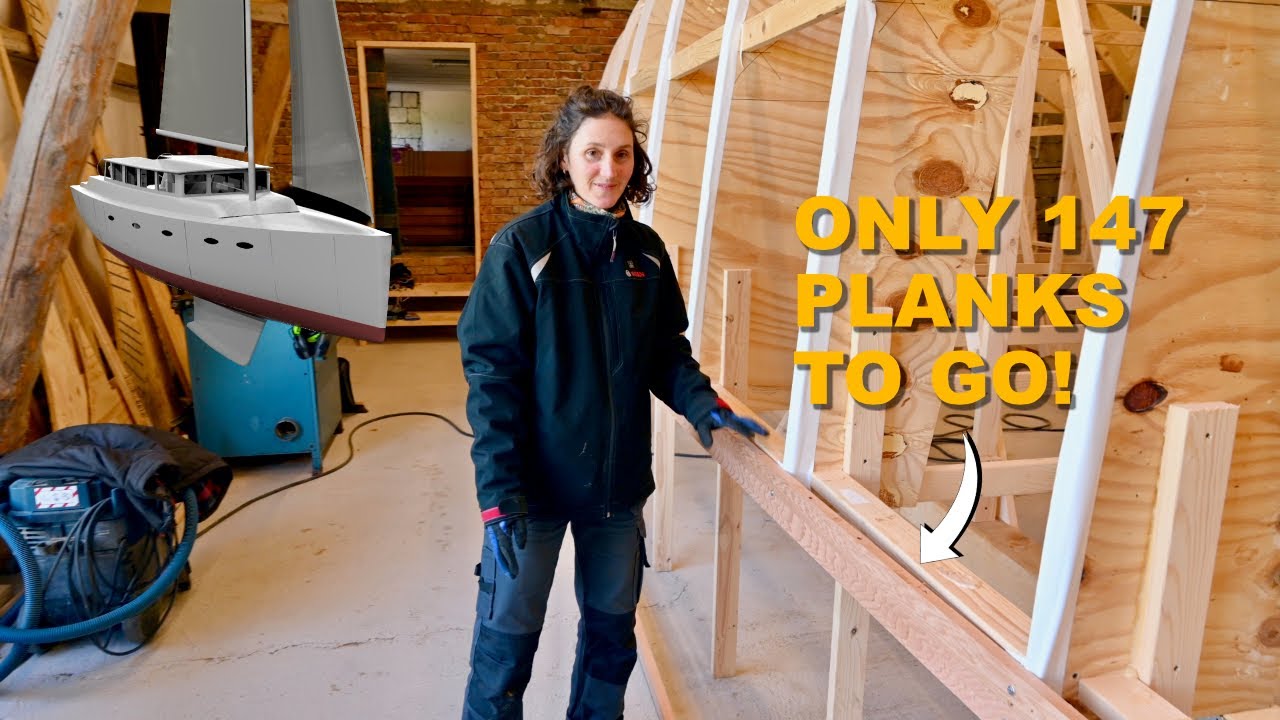
48 thoughts on “Prima dintre cele 150 de scânduri de bandă | Barcă cu pânze DIY 50 ft – Ep. 344 RAN Sailing”
Comments are closed.
Sorry for your loss. I'm sending you and your family my condolences. You're father has raised a great son and I believe he is proudly watching your fantastic project from where he is now 😊❤️
You might want to try making an insulated cabinet to keep your epoxy in. The heat from a 60 watt incandescent light bulb would probably keep the epoxy warm enough to pump easily. Just open the door, pump epoxy & hardner you need & close it back up.
Sorry for your loss. My condolences. May you have the srength to continue with your plans and build. I think that as you are building your dream boat – take the extra effort and use a 60 degree joint for better holding.
Condolences 🕊️
An excellent episode with a lot really great information…. and then the end. My heart just broke for you. I will be remembering the repose of your father's soul in my daily prayers. And peace to you.
⛵🌏💧🎣⛱🩳👙🐟🩱📸🐠🐠🌴🤿⚓🦀🦈☀️🇦🇺
Great video! Why not build a heated box for your epoxy like Mads did on Sail Life – plywood, foam insulation and a light bulb.
Condolences to you and the family
Our heart felt prayers to your family, Bernt raised truly amazing kids. ❤️ He remains in your thoughts and heart every day.
We love being a part of your year back on land, incredible successes and amazing progress on Ran III. With warm hearts of best wishes to you all.
My condolences. 🙏
So sorry to hear of your Father's passing. As everyone has said, he will have been immensely proud of his son and must have been delighted at how you are choosing to spend your life. As a grandfather myself, the gift of a grandchild that you and Malin gave him will have been such a delight as well. My condolences to you and your family and friends.
Thank you
When joining pieces of wood head on, I would go for at least 6:1, i.e. an angle of arctan(6) = 80,5° or more. For the spars of the wings I'm building, I use 10:1 (84,3°).
I'm very sorry to hear Johan has lost his father. Rest in peace. A big huge from Spain.
Warm water bath for the epoxy…I am sure you already thought of it. Cheap submersible heater in a barrel or even garbage can will do.
60 degrees 😉 Johan, are you going to bevel the strip edges when you get into the compound curves?
hurry up and build the boat, we don't need to be taught all the details
My sincere condolences Johan and Malin. I wish you all strength whilst dealing with your loss and wish you can look back on many nice memories you have made together. Thank you for sharing it with us. Our thoughts and prayers are with you and your family.
Johan. Great episode. Very sorry to hear of your loss.
Love your homegrown tests. Am very happy you chose the 60 degree joint.
This is so hard with the build and now Father grandfather has died. This boat will mean so much more now please take care keep going and I am sure he will be watching the build and making sure it is the toughest strongest best boat there is with you both.
Very sorry for your loss.
You're child is worth the little extra effort a 60% joint will take. Much stronger and the waste will be minimal but you'll know you've done the best for your family.
Sending deepest condolences to Johan and family for the loss of Bernt.❤
My opinion, go with 60
Sorry for your loss RIP Bernt
If I’m not mistaken Mads from Sail Life built a heating box for his epoxy during the cold weather. Perhaps DM him and ask or try to find it in his old videos. I’m sorry for your loss.
Hi Johan, Malin and Vera. I am very sorry to hear of the passing of your dad. Rest in peace Bernt.
Such a cool channel!
sorry to hear about your loss, my condolences.
For the scarf joints most boat builders are doing it like the lenght of the joint being 8 to 12 times the thickness of the planks, there must some really good reasons for this. Dont underestimate the hull twisting motion the sea will apply to it.
My wife and I are very sorry for your loss Johan. He must have been a great man to have such a great son. Our best.
I am very sorry for your loss. Sending love. May you find comfort in good memories.
RIP Johan's dad….he'll be looking down with such pride as the boat build progresses. God bless
Sorry for your loss.
A scarf join should be 8:1 brother. if you're joining 25mm thick timber, the scarf should be 200mm long, easy enough to make a sliding jig for the table saw to replicate it over and over, especially for the amount you are needing to do
🙏 Sorry for your loss 🙏
We are so sorry to hear about your father. Please know that you and your family are in our thoughts and prayers! 🙏🙏
Re: The mfg of the wooden dowel gun, that didn't respond to you. If you had used it, you would have been the perfect marketing tool. I was a buyer for a multinational copier mfg and have shown have encountered mfgs that have shown no interest in providing equipment or components that fit their current processes.
You have my sympathies I know how it feels
On another note the construction of my yacht is also strip plank but is done using a convex to concave join between planks glued and edge fastened with bronze screws and glassed on the outside only out of kauri timber and was built in 1974 and is still as strong and watertight as the day she was launched
This would cost a ridiculous amount of money to replicate now a days however
first sorry to hear about you father, you are waiting for stick to break, it will be very soon and when it does it startles you, me working for my father as a boy, cutting very tight corners with band saw, all day, and you here tick tick tick you know is going to break very soon, you are waiting for it then bang and it scares you ha ha
My Sincere condolences to Johan and family
Sending our thoughts and prayers at this sad time
Oooh was behind with watching So sorry for your loss Johan and family
RIP Bernt
The length of the joint should be 6-10 thicknesses of the board. This is a standard norm. 60 degrees are not enough. But perhaps the thickness of the fiberglass compensates for the lack of strength of the connection.
Rather than screws Why don't you clamp a short 2X4 to the bulkhead and use a wedge to hold the strips together. . Just remove the wedge to add another strip and re apply the wedge. Move the clamped 2X4 up the bulk head ever 3-4 strips and no screws to worry about and NO WOOD SPLITTING which will affect the trueness of the hull. You can do 20-30 strips a day with Marlin mixing epoxy and you laying the strip down and adding the wedges. Deffinatlly lay all the scarf joints up first as it will go much faster than doing each one as you apply the strip. I AM SO SORRY to hear about your Father. My condolences too you both. CHEERS TOO YOU ALL Steve h.
Since you’re glassing hull from both sides your strip planking is a core and you need only enough strength to bend plank on the jig without breaking. Without glass it would be a different story.
You probably don’t even need stainless screws. The core will be dry. In traditional wooden boats where screws were constantly exposed to salt water the galvanized screws worked for about 20 years before the hull needed to be refastened. In composite hull they would probably last forever.
Oh, I am so sorry for your loss. 😢 God bless
I think that overlapping joints by 4 inches would provide the best overall strength.