Sudarea unor plăci de suport din plăci de lanț robuste folosind oțel inoxidabil 316 reciclat pentru proiectul meu Wharram Pahi 42 Catamaran. Instagramul meu: @boat.fella Facebook: https://www.facebook.com/wildlingssai… Întrebări de afaceri: thewildlingsofficial@gmail.com Mulțumesc foarte mult oamenilor incredibil de generoși care folosesc linkurile de mai jos PayPal: https:/ /www.paypal.me/wildlingssailing Ko-fi: https://www.ko-fi.com/wildlingssailing Patreon: https://www.patreon.com/wildlingsailing Lista de dorințe Amazon: https://www.amazon.nl /hz/wishlist/ls/155FC0QR78BGF?ref_=wl_share Muzica pe care o ascult de fapt: https://open.spotify.com/playlist/22sIFakj1oGqZlpmXv3kgC?si=557a07debd3b4f64
source
Catamaranul meu salvat primește plăci cu lanțuri recuperate | Sălbatic Sailing
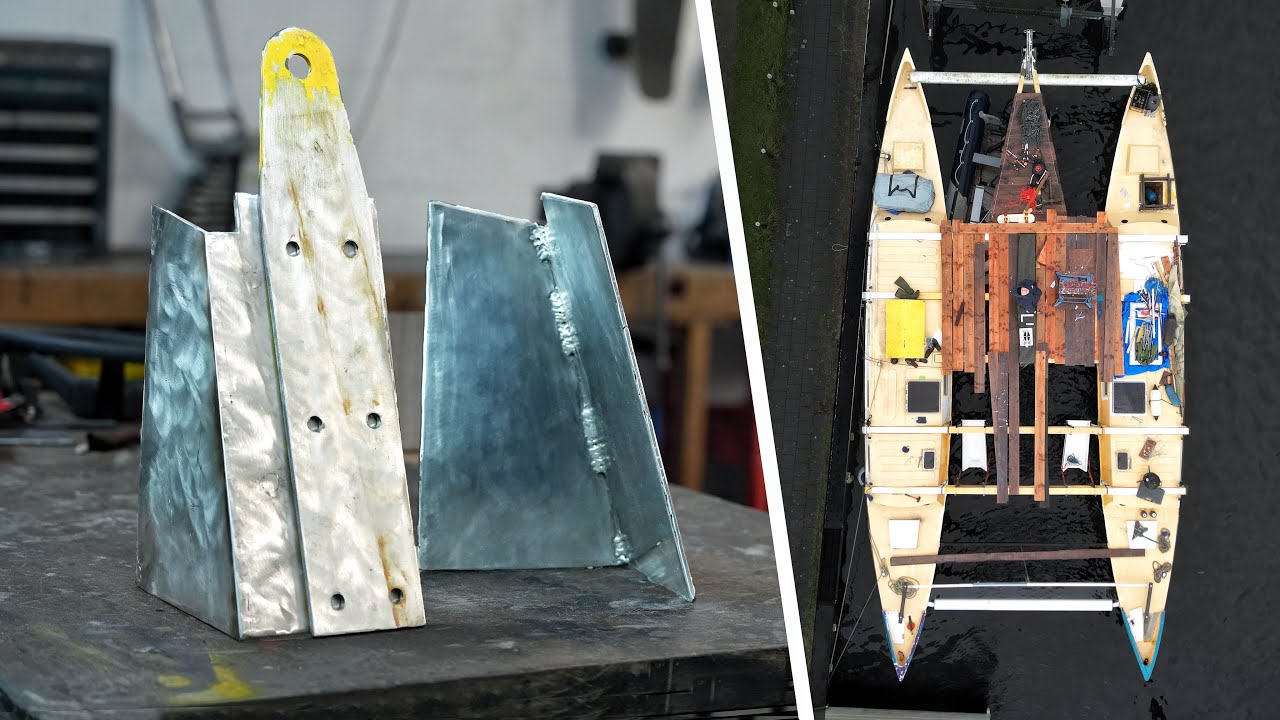
47 thoughts on “Catamaranul meu salvat primește plăci cu lanțuri recuperate | Sălbatic Sailing”
Comments are closed.
Great job less stress when blowing 50kts😅
Your dad is a great guy! I worked in metal fabrication for about 40 years, I’m sure I could have made the chainplates easier, but not necessarily better. That said, the rest of your dad’s mechanical skills far exceed mine! You’re a lucky man!
Great you learned welding, (better than i could do ) but SS backing plates are for force directly against the plate to spread the load from the bolts. Seeing as you’re going to have lateral load on the plates their impact will be minimal, 3 or 6mm thick doesn’t matter, and remain on the bolts against the ply inserts you’ve glued in. Best bet would have been to build up the cabin wall, bulkhead join and epoxy in reinforcing. The lateral load would have been far better spread due to the adhesion of the resin. Quite a bit cheaper to do it with epoxy as well if you count the purchase of the welder. Watch Duracell Project or MJ Sailing to see how they did their chain plate areas. They de-cored the hull side and laying layer upon layer of glass to build it up into a strong point. On my Fusion 40 (extended)cat I cored and glassed the bulkhead point to the boat side with about 15 layers of 600gm bi-ax/Uni each side. The inner and outer stays then connected to two SS straps that bolted together through the bulk head. Point is the strength is in the bulkhead not the stainless. They are the main load area on your boat and catastrophic failure point. If the mast comes down at sea you’re a little bit screwed! Sorry to be a negative Nancy but maybe time for a bit more reinforcing and to re-assess the SS backing plate load areas. Ask ANY boatbuilder, don’t take just my word for it! Sorry but you always ask for feedback. Long time fan!
Nice one!!!
Your welding has come along … nice beads along the edges. Did you mark out the locations of the holes on the template? It would probably be much easier to get all of the holes drilled with a drill press, rather than trying to go through 6mm of stainless with nothing but a hand drill back at the boat! Keep up the good work!
looking good, happy new year…
Two freaking weak good lord😔
If it works, it works!
Great to catch up with you again Mark and fantastic to see you fabricate the backing plates and learning new skills – life is a learning curve and one day you’ll be the one passing on the learnt and practised skills we’ve seen you gain and not just from this episode but from the whole project. Amazing to watch from a long term subscriber and liker of your channel and content
yo get work love the content !!
I get that this was a welding learning exercise, but if this was me I would have taken the plate to a mate with a bending machine & just bending two 3 mm plates !
Funny words I heard about welding: "A grinder and paint will make you the welder you ain't."
I would do some research into stainless steel, and how to keep it from corroding. I seem to recall someone, who seemed to know, saying stainless would rust if you scratched it, so my intuition would make me polish it. And paint it. And keep it away from the ocean, alltogether! 🙂
Love your dad is into full on muscle cars. Just like us in Australia 🇦🇺
It’s looking great….keep up the good work!
Good job. Did you think of making backingplates for the part that will be mounted to the bulkheads ? That also needs backing.
Great job marry, looking good
Built to last!
HAPPY NEW YEAR
I´m a professional welder and i thi9nk you did very well ! Respekt !
I loooove when you are complaining.. Thats how i learn what to think about when i go sailing..
Great that you have repurposed that 316 SS Mark, great outcome.
Hi Mark, I have watched all your videos, and would love to see more. I have also been catching up on the 5 years of content from Leo at Sampson Boat Co who has been restoring a 100+ year old gentlemans cruising yacht. H ehas 473K followers, god knows how many patreons and is now employing 4 full time boat builders to build his yacht in a covered hangar. His approach to everything is meticulous (maybe overly so), but also very eductaional. Maybe you can get some hints and tips from his channel and get your boat finished quicker. Maybe more videos (some general cat stuff?) means more income = more cash to buy tools, materials, services. Then you can speed up the project and get on the water sooner. Dying to see this boat go through sea trials!! Best wishes – Jon
keep it up dude. so glad i found your channel around the start of this project, been a joy to watch. also just an idea fron someone who knows nothing about boats, but those chainplates look like they could use a couple of horizontal strengthening brace peices across the 90°? would strengthen them and would stop them bending so much when welding the main seem weld…. lack of technical vocabularly on my part but hope it makes sense
Hey Mark, great work on getting those chainplates sorted out for Wildling! Your welding skills have definitely come a long way and it's awesome to see you improving with each project. Those backing plates might be overkill to some, but you know what they say, better safe than sorry. Keep up the fantastic work and keep thanking your dad for his support. You're truly lucky to have him. Wishing you smooth sailing ahead, my friend.
Looking good mate! Great work on the welding. Make sure get a good looking wheel for her
1 a week we don't care what your doing
Great work mate plenty strong. You might think about a sheet of fibre glass on the inside of the Hull larger than the repairs you did.
Great job! Nothing stops you 💪
Well done, man. Plus, working with your Dad has to be special.
As a dad when I see footage of you working with your dad and uncle in his garage my heart fills up. Great videos. ❤
Well done Mark. Your skills are certainly getting you used to some new techniques which will stand you in good stead later on. Some great work carried out at home. Well done.
Awesome work Mark and your dad of course, he is a legend. If the backing plates are overkill then you won’t be worrying about them whereas if you just went with the 3mm you might have had a nagging worry in your head and I’m sure there will be plenty of other things to worry about. As for your welding, it looks great to me, I’m no expert but yours is a million times neater than mine. Look forward to the next video. Andy UK
Great job, keep it up
Please ask your father to correct the orientation in which he is hanging the US flag. I appreciate his liking American muscle cars, but seeing the flag hanging incorrectly is bothersome
Keep going. I look forward to seeing your videos
enjoyed this episode
Some of the welds needs more heat for better penetration, more so when you welded the 6mm plates to one another. But will still be plenty strong, keep up the good work!
Happy New year, all the best! So looking forward to the next video
Welding looks good given your limited experience and especially with stainless
Great job
Mark, you're getting to be a dab hand now at all this engineering milarky !! 😊. You actually look good holding these tools now. Its great to see. Still a massive task ahead of you but You got a great team behind you and were all willing you to get it done and have faith in you. Well done you. 👏 👍
Nice work Mark .
th
Happy New Year to you and yours, enjoyable as always. Thank you.
Enjoy your family and glad you’ve got the chance to make the chainplates going.
Today the youth dont learn from their fathers as most dont want to do garage work only finger pushing on cell phones. .
Hi Mark,
Great work keep it up.
A little note.
With stainless steel any steel touches or scratches the stainless it will rust where steel touches.
All grinding discs should be iron free as well or will rust the stainless.
When was work in a stainless workshop no mild steel aloud in the stainless shop.