Acest canal de Youtube este despre mine, un marinar solo dislectic de 83 de ani și 2/3 de ani, care construiește o canoe de 20 de picioare pentru o croazieră lungă la latitudine mare. Dacă sunteți interesat să contribui, linkurile sunt mai jos. https://www.paypal.com/donate/?hosted_button_id=53X8NVEA22MBL Swish 0706200550 De asemenea, abonați-vă Pentru mai multe vedeți Yrvind.com
source
1 ianuarie 2023. 7X17X17= 2023. Bara plată din aluminiu a scăpat mult înapoi, creând o problemă interesantă.
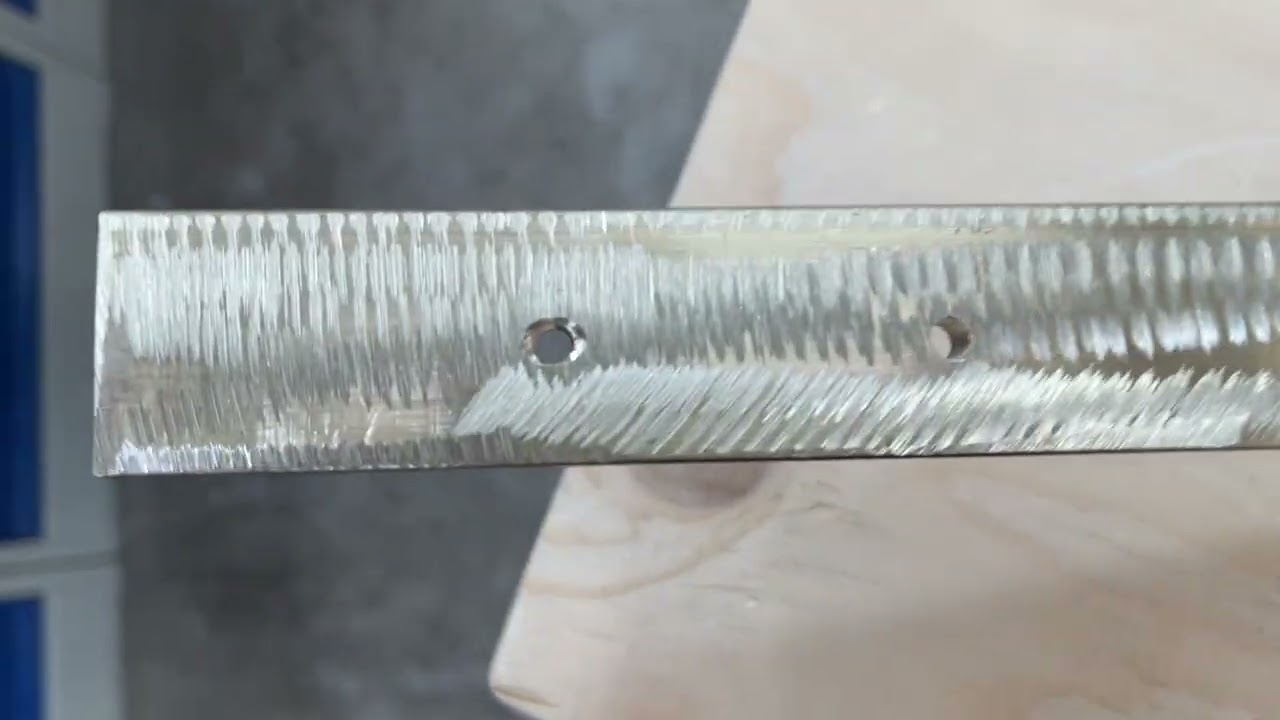
29 thoughts on “1 ianuarie 2023. 7X17X17= 2023. Bara plată din aluminiu a scăpat mult înapoi, creând o problemă interesantă.”
Comments are closed.
Happy new year 🎉 😁👍
Great Video to start out the new year! 🙏❤️🇺🇸👣⛵️🥳
with all that spring-stored energy, orca will surely be surprised after biting the rim off..
I do hope this will keep it’s shape and not spring away 🤞🏽
Get a hold of a blow torch , and heat it in the vice? I think all that spring energy is nothing that will work in your favor. 4-500c or something should be enough?
I wouldnt want to bite it……
I wonder if a blacksmith would be able to form the aluminium bar to the correct shape?
By using a forge and hammering??
Aluminum Bronze, right?
Put it back on the buck and heat the whole thing with a propane torch to 350 to 400 degrees fahrenheit and let it sit until cool. You'll want to do that outside for all the smoke. I read that it takes around that temperature. I put the website of the heating of the alumi-bronze in your comments section here about 3 or 4 weeks ago when you were discussing it. That heat gun wouldn't get it any where near that temp.
if you are going to glass over it…then the screws cant "boing" out some worst time later.
Dr Yrvind; Orcadontist…
What about laying it over a large diameter pipe, and peening the outer surface? That should stretch the outer side and allow a tighter curve.
Maybe bend it over a smaller radius form so that even when it springs back it is nearer the desired shape? But perhaps it is too late for that now.
If the bar is aluminium then the epoxy is unlikely to form a long lasting bond unless you wet sand the bonding surface with catalysed resin. Otherwise the aluminium oxidises extremely quickly giving a poor bond.
There are specific tools for forming a symetric arc form. The Swedish word is kallvalsning.
Probably would bend cold using a pipe bender that can handle flat stock. Drill the holes afterwards so not to create weak spots. You could bend it right to the frp shape…just work it a little at a time. until you have the perfect fit.
I wonder if using a needle gun on it while tensioning . Think 20-30 little hammers tapping 10000 times a minute. I know it's done to harden metal would relieve tension enough to reduce aid in bending
Du kan fråga smeden Torbjörn Åhman på Youtube. Nog bra att helt få bort spänningarna. Han finns i småland också tror jag.
Cut kerfs (shallow grooves) in it every few centimetres.
cold bend the bronze, and you'll have better luck. No heat!
Heat will make it fracture, just over bend it.
It would make me nervous thinking about that bar forever exerting that much tension trying to break loose and spring free. Personally, I'd try to deform it more. Perhaps by simply standing on one half and pulling on the other end.
To soften bronze heat and cool quickly. To harden heat and cool slowly.
I Will heat it to a high temperatur with a gas bruner to g’et the tension out.
I agree with the comments below. That will always be under tension. Perhaps take it to your friend at the foundry.
Im a metallurgical engineer, specialising in marine structures. I can tell you that your aluminium bronze can be cold worked with some risk of cracking and it requires large forces which you may not be able to reach in your workshop.
It can also be hot worked and its suitability for hot working is good. The best temperature for hot work of aluminium bronze is between 780 – 870 deg C. You will need something more powerful than an electric heat gun because of coppers extremely high thermal conductivity, meaning your heat source is rapidly drawn away and dissipated to the atmosphere. Insulation will help. You only need to reach high temperature in the area you are bending, not the entire piece. You can confirm that you have reached the required temperature using special crayons which change colour when temperature is reached. They are commonly used in critical welding operations, so can be procured there. Hope that helps.
Happy New Year! I wish I could support monetarily, but at the moment I can contribute comments and likes. I’m truly grateful for your work and all that you share! Keep up the inspiring channel, and big thank you to Peter and friends.
A heat gun is not hot enough. Jou have to heat it with acetylene burner and a steel Mal
The aluminium bar is best annealed before bending to shape, or it will spring back or just have too much tension.
Usual method for aluminium car body work is to soot the panel with a pure acetylene flame, then heat until the soot just has disappeared. It is now annealed and ready for straightening of the dent.
Good luck with your build and sail!