Alăturați-vă echipajului RAN Sailing ~ pentru streamuri live, conținut exclusiv și multe altele https://www.patreon.com/ransailing S-ar putea să sune puțin, dar suntem atât de fericiți că am plătit 16% din carenă! Facem și o mică pauză și arătăm cum arată ferma în plină primăvară 😊 Suntem o familie suedeză care a navigat prin lume din 2016 în timp ce împărtășim aventurile aici pe YouTube. În timp ce încă navigăm, obiectivul nostru principal acum este construirea RAN III, o barcă cu pânze de 50 de picioare pe care o construim de la zero. Postăm un episod nou în fiecare vineri, așa că asigurați-vă că vă abonați și apăsați clopoțelul pentru a fi primul care află când există un nou episod! CONECTAȚI-VĂ CU NOI – Site: http://ransailing.se – Instagram: http://www.instagram.com/ransailing – Facebook: http://www.facebook.com/ransailing PRODUSE ȘI CAMERA: https:// www.amazon.com/shop/ransailing Am adunat unele dintre produsele pe care le folosim în viața noastră de croazieră și realizarea de videoclipuri în magazinul nostru Amazon. Dacă cumpărați oricare dintre articolele din magazinul nostru, primim un mic „ka-ching” în pisicuța noastră de croazieră (fără costuri suplimentare pentru dvs.). Mulțumesc mult și mulțumesc programului Amazon Influencer. Credite muzicale: http://www.epidemicsound.com Love, Malin, Johan & Vera
source
16 % dintr-o cocă cu scânduri – DIY 50 ft Boat Build – Ep. 346 RAN Sailing
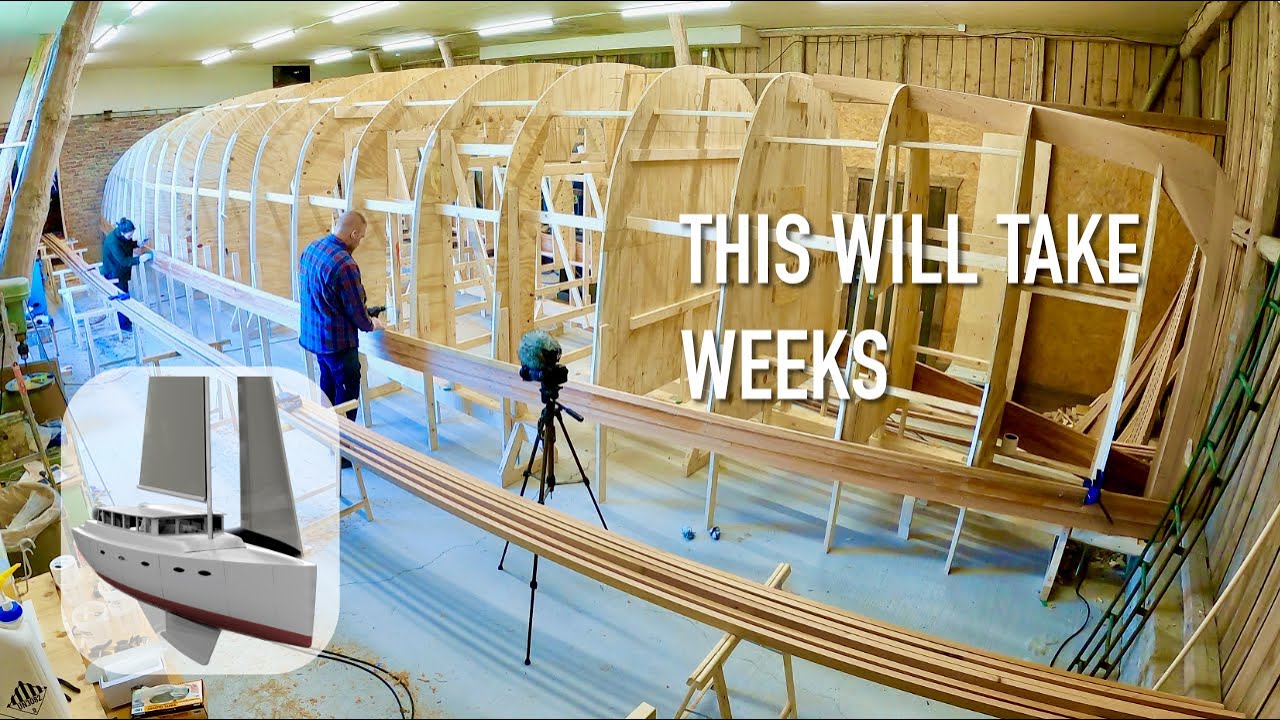
Make everything so stable that orcas can't harm the ship later….!!
I just saw a video of Orcas sinking a 39 foot French serial yacht;!They had ripped the rudder out;!
👏🏻👏🏻👏🏻
She (RAN III) Is shaping up nicely. Good work, guys. I must admit though, with all the talk from Malin about land stuff around the farm, makes me wonder if she will get too used too that 🤭 not to mention resources required. 🤫🤔
I have asked this question a few times without any reply (I know they are really busy). I was just wondering if it would be helpful (faster) if they allowed people to come out and help them (volunteer). Does anybody know the answer? Thank you and thank you for another great video.
Well done 👍. Question, what is the process for removing the fasteners holding the planks to the forms?
Terrific video as always …❤️
My wife and I took 6years full time to build our 12.8 M sail boat . See u/tube Brychan l l keep going spend less time filming.Cheers TonyVal
You live in a beautiful place. I like the pictures of the pheasants and deer in the fields. Your daughter is a beautiful and lucky girl. I love watching as your boat coming together. It's an amazing project.
Very great job! It's a pleasure to follow your project unfolding. I hope you are able to valorize the sawdust for heating purpose for instance. All the best for the work ahead. GOD Bless!
Instead of passing the planks over the top of the hull (which looks a bit precarious) have you thought of making two little holes in the end wall, pass them outside through one hole and then back inside through the other?
how wide are those strips?
Seeing you rip through cedar reminds me when I was young with no respirator. Had great ventilation all doors open. Wasn’t the pine or oak that has to sharpen many blades before. Time spent on calculating the percentage of work done. Think that number be higher if spent working then calculating lol. What a great couple with a little job site inspector. One stick at a time it will be done.
What price that moment for a parent? 5:45 – 5:51
Wait a minute. Wasn't your daughter a newborn like Yesterday? 😳 My Oh My how time flies.
Enjoying the boat build. Can you show us some good close up vision of the joins, screwing or planing of the joins.
Do the boards overlap? Or do they sit on top of each other. It is very hard to see.
It is all a little one dimensional for me at the moment.
Kämpa! Ni är så jävla grymma! Det där börjar ju faktiskt likna en båt! KUL!
Set up a simple pulley to move the strips over…. you're going to break your leg :p
A suggestion for lifting and lowering the planks.
Screw 5 large Eyelets (say, 30mm inner diameter) into the ceiling of your boatshed along the centre line of Ran111, and using 8mm braided rope run lines through them. One end to hooks made of plywood to hook around the individual planks, and the other end to a central point by the laying up sawhorses. With the aid of a boathook (or, of course, a batten with a notch cut in one side and a screw put in the other, you will be able to lift planks up to the keel on your own, lower them onto the keel, allow a little slack and pull them over and down the other side a little (using the boathook), then returning to the common point, lower them down all one person operation!
That is it, no more excuses, now Johan can work 24 hours a day on his own, all Malin has to do is throw a sandwich into the boatshed every few hours, and Ran111 will be planked in no time!
Vera is visibly growing and learning so much every week!
What thickness is the completed cedar strip? Nice progress!
Hi,
I am following your project since day one. Sure you are going great.
Could you please inform me about planking thickness??
One more thing, you are using wood for planking, would it be more easy to use foam??
Same like this YouTube channel: SailingSVLynx??
Thqnks
farið að líta út eins og Víkingaskip 🙂
Good teamwork. The old farm machine is a dump rake, designed to pull behind a team of horses to gather hay into rows.
Just a quick question……As you plank around to the bottom are you going to have to angle the sides of the planks to match the curve from the side to the bottom of the boat? It seems like you would leave gaps of you used a square edge on the sides of the strips as you made the transition from the side of the boat to the bottom of the hull. Am I wrong?
The little one is Beautiful
Brilliant! So exciting watching the hull develope before our eyes. As usual great video .. thank you.
The stuff! Thank you
High time for another lovely baby
You are very inspirational. Amazing
Ask someone to park their goats on an area of ground elder weeds, they will get them taken care of in a day or two. Also it's a great way to make connections with locals, especially if goats belong to a local family who wouldn't mind free feed area for their goats
Hello, Do you need relevant government documents to go to sea for the sailboats you make yourself? Or can it go to sea after the construction is completed?
they have used a plastic nail gun to hold the planks in place rather than screwing them in – the plastic nails can be left in – this would save you a lot of time
Hey can't you use just normal waterproof wood glue at this stage. Not epoxy? It would be way faster cheaper and as far as I know just as strong? The glue joint is only as strong as the wood around it and with ceder normal wood glue is way stronger. Wood glue sets in 45mins.
1. That’s a fine proper Fort if ever there was one. 2. What is an ice cream boat?
Great Video !
Hello Malin, Johan & Vera,
Thank you for sharing the stories of your adventures on the water and in boat building. My family and I have been enjoying the videos.
At present, we are refitting a cold-molded aero-rig sailboat named Fly that was built in the UK by the Elephant Boatyard in 1991. The yard was one of the early adopters of West System construction with red cedar strip planking for larger sailboats. The hull construction of this boat and rig has some ideas you might consider for your build. The hull layup on Fly is similar to what you are proposing: red cedar strip planking edge glued with West System epoxy and then several layups of vacuum bagged fiberglass inside and out.
Here is the first suggestion: on the interior, the hull is covered with two layers of nylon ballistic cloth which is glued in place in such a fashion that it can release. The idea is that an impact, especially with a sharp object (e.g., corner of a shipping container) might penetrate the fiberglass layers, but the cloth will release and prevent water ingress. This is similar to the construction of Greenland kayaks and Aleut baidarkas. What is more, the nylon cloth gives the interior a very nice finish. See the photos of the aft-quarter berth on Fly: https://www.mcyachts.co.uk/news/new-listing-70-ian-howlett-elephant-boatyard-aerorig-fly/
Here is the second suggestion: the Appendix for Gudgeon Brothers on Boat Construction gives data and several charts for fatigue that are quite revealing (pp. 379 ff). Consider the differences of wood and epoxy, fiberglass composite, and carbon composite. Wood composite performs considerably better than fiberglass alone due to cycles of flexing. One round the world trip may fatigue fiberglass to only 20% its original strength, whereas the wood will retain about 55%. The Gudgeon brothers point out that this loss of strength will continue with additional use. Carbon, on the other hand, will retain about 60% of its strength in the direction of the fibers indefinitely. As such, you might consider adding some layers of woven carbon along with the fiberglass. Proof of the long life of a carbon layup can be found in the freestanding carbon masts made by Carbospars (as on Fly) and Magma structures (on boats such as Black Pearl). If you intend to cruise in the higher latitudes, then you might consider some exterior layers of carbon woven with aramid fibers.
Best,
Jeff
Make a couple holes in the wood wall to transfer ceder strips to the other side???
awesome video as usually , many thanks
Keep going guys !👍
Hej Malin och Johan,
Lite off topic, men jag har liten fundering. Har nämligen köpt mig Wauquiez 40 Pilot Salon och behöver hämta henne till Helsingborg från Porto i Portugal. Undrar om ni har lust att ta en liten avkoplare och hänga med åtminstone genom Biscaya och Engelska kanalen 😅 Självklart står jag för alla kostnader. Planerar att börja passagen runt 20de maj
Loving the new boat build,can’t wait to see how it turns out,well done to you guys 👍
How do you attach the strips to the stem? 🤔
Thanks for posting and sharing. Great to see the strips going on.